1 WELDED FABRICATIONS
1.1 SCOPE
This specification defines the minimum requirements for the welding and inspection of welded fabrications and steel structures when supplied as part of mechanical equipment.
2 PROCEDURE QUALIFICATIONS
Welding procedure qualifications and welder performance qualifications shall be carried out in accordance with:
• ASME IX and
• AWS D1.1
AWS D1.1. Prequalified permitted only on fillet welds or partial penetration welds, full penetration butt welds shall be supported by a PQR.
Note: ISO/EN codes may be accepted at the discretion of the Engineer.
Welding procedure specifications and procedure qualification records shall be submitted to the Engineer for approval prior to the start of welding.
Weld processes acceptable to the Engineer, provided they are qualified, include:
• Gas Metal Arc welding (GMAW)
• Shielded Metal Arc welding (SMAW)
• Gas Tungsten Arc welding (GTAW)
• Submerged Arc welding (SAW)
• Flux Cored Arc welding (FCAW)
• Surface Tension Transfer welding (STT)
Any other process is subject to the approval of the Engineer.
3 HEAT TREATMENT
Preheat temperatures shall be established in procedure qualifications or when specified in the applicable code of practice.
When preheat is mandatory for welding, the preheat temperature shall also apply for tack welding.
Post weld heat treatment, (PWHT) where required, shall be carried out in accordance with the relevant procedure and specification.
All PWHT procedures shall be submitted to the Engineer for approval before work is started. Testing shall be done on the heat-treated item to confirm its compliance and not on a similar piece of material treated at the same time. This shall be done by allowing for an extension of the component, of the same dimensions, which is cut off for testing after heat treatment. These will be regarded as coupon plates.
Stress relieving shall be performed as required on the drawings which shall state the required
temperature and time at that temperature, the maximum or minimum heating and cooling rate in EC per hour.
Records shall be kept of the temperature and heating cycle. A current calibration certificate of the furnace instrumentation shall be produced on request prior to the material commencing heat treatment.
4 CONSUMABLE REQUIREMENTS
Only welding consumables complying with a recognised classification system shall be used for production welding.
Consumables shall be stored in clean dry conditions to prevent moisture pick up and mechanical damage, electrode types shall be separated and identified for type and size.
Where required, electrodes shall be baked in accordance with manufacturers’ recommendations.
All electrodes that undergo baking should be issued in accordance with a procedure that will record all baking details. “Hot boxes” shall be used for manual metal arc electrodes low hydrogen types E 7018, E 7015, E 7016, and E 7024.
5 WELD JOINT PREPARATIONS
Surfaces to be welded shall be smooth, uniform, and free from tears, cracks, or other defects that would adversely affect the welding quality or strength of weld surfaces. Surfaces adjacent to a weld shall also be free of loose or thick scale, slag, rust, moisture, grease, paint, or other foreign material that will prove detrimental to weld quality.
6 TACK WELDS
Tack welds shall be subject to the same quality requirements as the final welds except when tacks are not to remain as part of the weld.
Tack weld’s, which are incorporated into the final weld, shall be made with electrodes meeting the requirements of the final welds and shall be thoroughly cleaned. Multi-pass tack welds shall have cascaded ends. Tack welding shall only be performed by fully qualified welders on all equipment other than structural steel and platework.
7 CONTROL OF DISTORTION AND SHRINKAGE
In assembling and joining parts of a structure, or build up of members, and in welding reinforcing parts to members, the procedure and sequence shall be such as will minimise distortion and shrinkage.
Insofar as is practicable, all welds shall be deposited in a sequence that will balance the applied welding heat whilst welding is in progress.
The direction of the general progression in welding on a member shall be from points where the parts are relatively fixed in position with respect to each other towards points where they have greater freedom of movement.
Joints expected to have significant shrinkage should usually be welded prior to the joints where less shrinkage is expected and with as little restraint as possible.
In making welds under conditions of severe external shrinkage restraint, the welding shall be carried out continuously to completion or to a point that will ensure freedom from cracking before the joint is allowed to cool to below the minimum specified preheat temperature.
8 VISUAL EXAMINATION
All welds shall be examined for acceptable weld profile and finish. The weld shall have uniform contour and be free from large ripples.
Fillet weld leg lengths shall not be less than the values required by detail drawings and shall not differ from each other by more than 1.5 mm. Joints at all external stop-starts shall merge smoothly and shall not show a pronounced hump or crater in the weld surface.
Intermediate undercutting is permitted provided that the depth does not exceed 10% of parent metal thickness or 0.8 mm whichever is the smaller.
Incomplete filling of butt joints is prohibited. Butt welds shall have uniform convexity to a maximum height of 3 mm or t/5 whichever is smaller, where “t” is the thickness of parent material. In butt welds there shall be full fusion, along the length of the weld unless the relevant specification allows a certain length.
Provided there is complete root fusion, root concavity is acceptable if the thickness of the weld is not less than the parent metal.
The weld surface shall be free from cracks, porosity, shrinkage, cavities, and slag. The weld surface and adjacent parent metal shall be free of arc strikes, chipping marks or weld spatter.
9 NON-DESTRUCTIVE TESTING (NDT)
NDT, where required, shall be carried out in accordance with a recognised code of practice with procedures and qualified personnel.
Acceptance standards shall be in accordance with the relevant specification.
All NDT procedures and operator’s qualifications shall be submitted to the Engineer for approval. Operator qualifications shall, as a minimum, be to acceptable international qualifications.
10 MACHINING
Machining shall be accordance with the drawings. Any deviation there from shall be approved by the Engineer in writing.
11 CORROSION PROTECTION AND PAINTING
This shall be done in accordance with the following DRA project specifications:
• SPXXXXXXXX – Corrosion Protection and
• SPXXXXXXXX – Colour Coding and labelling of Plant.
12 INSPECTION AND TESTING
Inspection and Testing shall be done in accordance with the requirements of the order and the Quality Plan where applicable.
Where the following procedures are specified, they shall be done in accordance with the standards as listed below:
12.1 RADIOGRAPHIC EXAMINATION
ASME V 2007, AWS D1.1 2006.
12.2 ULTRASONIC EXAMINATION
ASME V 2007, AWS D1.1 2006.
12.3 MAGNETIC PARTICLE EXAMINATION
ASME V 2007, AWS D1.1 2006.
12.4 DYE PENETRANT TESTING
ASME V 2007, AWS D1.1 2006.
Other internationally recognised standards may be used at the discretion of the Engineer.
12.5 FINAL ACCEPTANCE
All the acceptance parameters shall be demonstrated by the Vendor and witnessed by the Engineer. When all the requirements have been met the Vendor shall provide written records of the testing to the Engineer who shall then accept the equipment as complete.
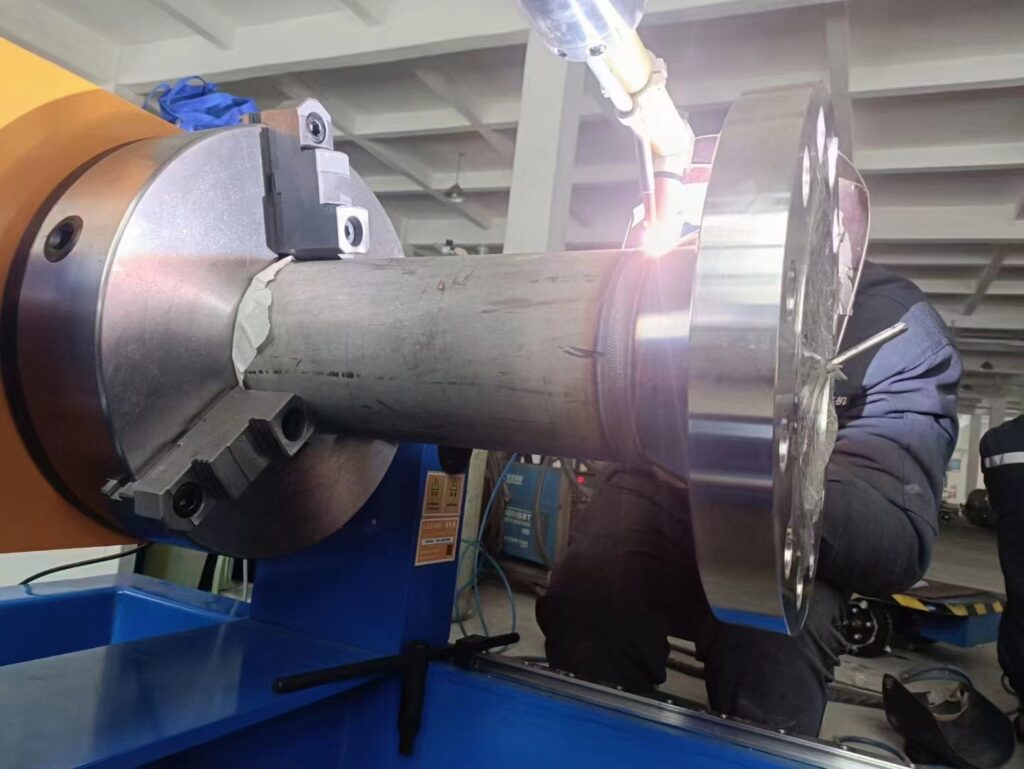