The current domestic anti-corrosive steel pipe adopt epoxy coal tar anti-corrosion, welding epoxy powder(FBE, glassfiber anti-corrosive) and three-layer PE, anticorrosive, but from the anti-corrosion structure should be the first choice.
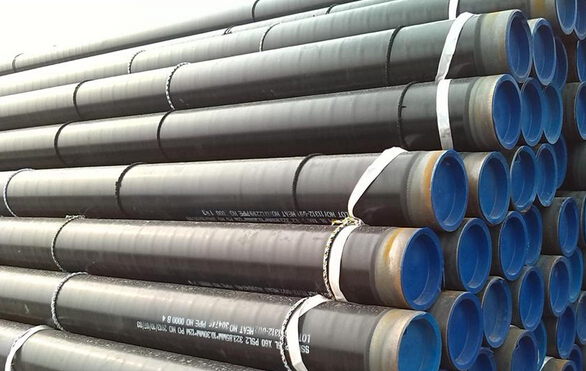
Structure of three layer PE anti-corrosive pipe
Three layer PE anti-corrosive steel pipe carry out the national standard GB/T23257 – 2009. Anti-corrosion steel pipe with inner layer of epoxy powder coating, middle layer of adhesive, outer layer of polyethylene.
Technological process of three layer PE anti-corrosive pipe
1. Shot blasting degusting processing for the steel pipe
Before shot blasting degusting, with medium frequency induction heater, the steel pipe should be preheated to 40-60 degree, and then through the shot blasting machine to remove the water, oil and dirt contamination, derusting grade is up to GB/T8923-1988 standard, Sa2.5 level (nearly white level) requirements, the depth on the surface of the steel anchor pattern from 40 to 100 microns.
2. Epoxy powder coating
Before spraying, the steel pipe will be wrapped in kraft paper on both ends, then use medium frequency induction heater, heated the steel pipe to 190-230 degree, the electrostatic spraying method is adopted to epoxy powder as required amount of powder coating to the steel pipe surface, in the high temperature, combination with base material fastness, its anticorrosion performance is superior, the good resistance to chemical corrosion, coating surface density is smooth, wearable, and anti-high temperature.
3. Extruded adhesive
According to requirement of the thickness of adhesive layer and polyethylene, by adjusting the extrusion machine lord motor and screw revolution, to meet the requirements of extrusion amount. When the epoxy powder in a gel form, we adopt lateral winding technology, make the adhesive and PE coated on steel pipe, adhesive epoxy powder, polyethylene polymerization to form a three layer structure, after molding, with three rows of roller, make three layer structure fusion compaction, make it a whole system with smooth surface, without bubble and defect.
Adhesive performance is stable, strong adhesive force, uniform film-forming.
Temperature of PE extrusion is 230-260 degree, PE aging corrosion resistance is strong, good environmental stress cracking resistance and elongation properties.
4. Cooling of coating pipe
According to the requirements of the three layer structure of the material properties, it requires slow cooling, temperature of cooling pipe should not exceed 60 degree.
5. Jeeping
In the production process, using online electric spark leak detector for coating 100% of leak detection voltage is 25 KV. It requires no funneled under 25 Voltage leak detection.
6. Coating products processing
Use groove grinding machine for pipe end for processing and tags.
Main materials
Epoxy powder adhesives and polyethylene epoxy powder material, for example, FBE form American 3M company, Dupont resin adhesive and domestic high quality polyethylene materials.